Sand control challenges can occur over the life of the well, from initial completion design to failure of existing downhole equipment, or in later life, due to increased water production. Regaining sand control integrity in existing completions is now a more pertinent issue to overcome. In cased and perforated completions, careful consideration needs to be given to either installing sand control products in the early stage of the well or, alternatively, incorporating the option later.
New sand control technology. To address integrity problems, a new-generation sand control technology has been developed by Tendeka, a TAQA company. Filtrex, a through-tubing remedial solution, boasts a unique filter mechanism comprised of a conformable open-cell matrix polymer (OCMP), Fig. 1. It was recently deployed across a three-well campaign in the shallow waters of Mahakam field, Indonesia, for PT Pertamina Hulu Mahakam , which had been experiencing numerous sand control issues, mainly, erosion, pass-through and plugging. Overall, the OCMP filter had a positive effect on sand retention and delivered improved well performance. Following on from the well campaign, the technology is undergoing further improvements for use in gas wells requiring sand control that expected early water breakthrough. Germ cyclone
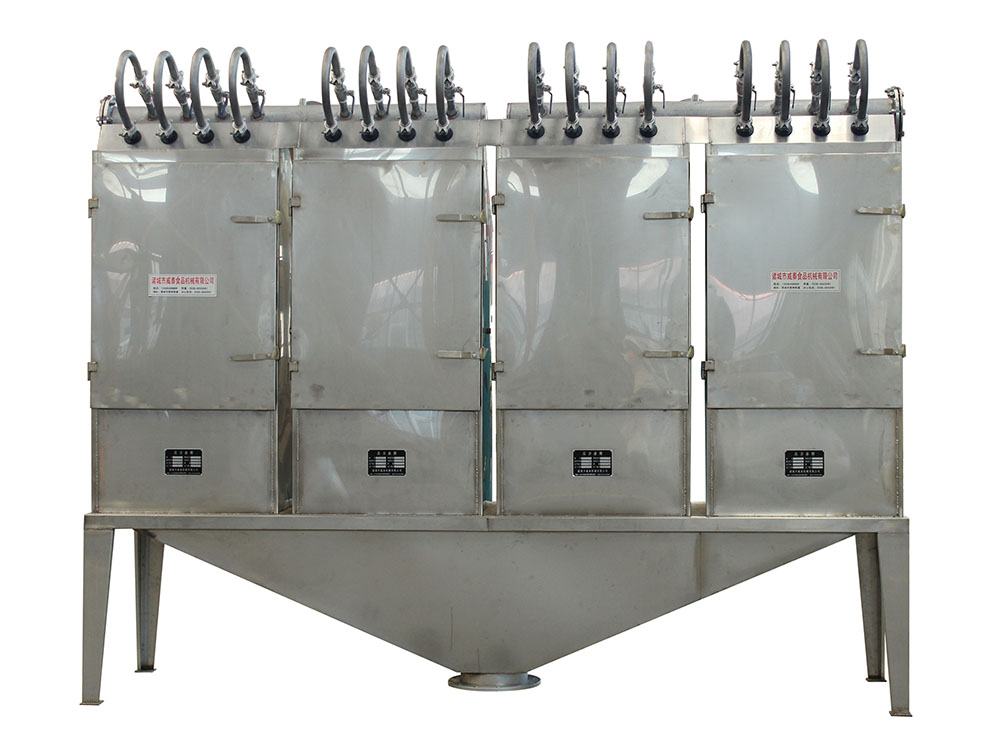
Novel through-tubing remedial solution. Using similar sizing to the predicted sand generation in the field, the aim of the laboratory and field evaluation was to assess the suitability and performance of the OCMP filter, using both outcrop and reservoir sands, Fig. 2. The OCMP filter was selected as an alternative to a mechanical screen, to address pass-through and plugging challenges, due to improper screen slot opening size and high uniformity coefficient (UC).
The OCMP is a multi-layer design, with up to 85% porosity and 43.4 Darcy permeability. The technology is run-in-hole, compressed within a sleeve via coiled tubing or slickline, where it can be deployed along with an integral anchor system or latched into retrievable set packers. Once set, the filter media will return to natural shape and size to conform with varying wellbore IDs. This allows transit in tight restrictions within the upper completion whilst also setting and conforming to larger casing/screen IDs, where control of sand has been lost. The OCMP filter conformance completely fills the annular gap, preventing further solids ingress into the wellbore, thereby reducing the impact of any potential further erosion and plugging failures. 1
As there is no change to the OCMP once deployed, the pore size and shape are known prior to deployment, enabling an accurate understanding of its performance in well environments. With a range of sizes to cover a broad range of applications, once installed, the tool requires no further intervention but can be retrieved easily later, if desired.
During deployment, a compression sleeve completely protects and compresses the OCMP until at depth, when the sleeve is removed. After removal of the sleeve, the OCMP expands and conforms back to its initial size and shape. As the tool can self-centralize, it can be used in high-deviation wells. The OCMP is adhered to an optimized base pipe, which is not limited to standard API base pipe sizing. The base pipe, itself, is designed specifically to support the OCMP in high-rate environments.
Operator challenge and methodology. The strategy of Mahakam field is to produce from shallower intervals in unconsolidated formations, in both oil and gas reservoirs that have a limited producing life. 2 Therefore, embedding a sound sand control approach is paramount. Pass-through and plugging were common challenges in the field, related to the particle size distribution (PSD). So far, there was no established screen that could tackle sand issues related to the PSD dependencies. Meanwhile, erosion was caused by the high production rate. Conventional sand consolidation treatments, such as through-tubing screens and gravel packs, as well as erosion - resistant screens , had been installed with varying success.
Three wells were assigned for sand control intervention. All three wells (two were from different fields) had the same well architecture, 3.5-in. 9.2# (2.992-in. ID) cemented monobore perforated casing completion, with a minimum restriction of 2.81-in. ID. Due to the short lifespan of the production intervals—between three and six months—it was critical to recover as much oil or gas before the zones watered out and with the lowest skin possible. The target of the OCMP was to provide sand control integrity beyond the duration of other solutions previously implemented.
During retention tests in the laboratory, the prepared formation sand slurry is pumped and diluted with water before being flowed through the compressed OCMP filter. Pressures are then recorded over time to monitor pressure build-up to indicate whether the OCMP filter is providing adequate retention and/or is liable to plugging during the trial.
The effluent samples collected were filtered through pre-weighed 1.2μm filter membranes, which were dried and then reweighed. The pressure data and sand-through data results were collated and represented graphically for interpretation alongside image analysis of the grains passing the filter. Most of the sands were sorted with D10 values c.250-300 microns. However, there were other challenging exceptions including poorly sorted and bi-modal distributions.
Both outcrop and reservoir sands were chosen to represent the PSD across the data provided, covering a range of particle size distributions that could be encountered within the targeted wells. There were two outcrop sands (sand mix 4 and mix 5): the first was poorly sorted sand with a high fines content, while the other well was sorted with a lesser D10 value and fines content. The reservoir sample chosen was very poorly sorted and had fines with >30% grains less than 45 microns. The PSD of the sands was measured by dry sieve analysis.
OCMP sand retention results. In line with manufacturing and operational requirements, the OCMP filter was compressed to achieve optimum sand control effects. During this evaluation, the sand-through retention tests performed were low, and the sands were very well-retained. To further qualify the retention performance of the OCMP filter, a comparison was made of the change in sand-through with time and the pressure profile. In essence, sand control is achieved, if the sand-through data quickly drop to a low level during the test. If control is poor, then significant amounts of sand will continue to be produced during the test. The pressure drop observed will be a combination of the sand permeability and any plugging of the OCMP filter—the filters themselves are too permeable to generate any significant pressure drop.
Therefore, the pressure profiles for a particular sand should be similar on each polymer filter, given good retention and no plugging. At the end of the retention test, sand injection is stopped to perform a swab-and-surge-style test to help identify any plugging with the filter. The flow of clean water is started and stopped at regular intervals, and the pressure is observed for any inconsistencies. Figures 3-5 show data obtained using the test sands, which demonstrated good results.
More sand passes through the filter initially with sand mix 4 and fine reservoir sand, due to the higher percentage of finer material but it falls away to lower levels in line with the other test sand (sand mix 5). The pressure profiles recorded during testing also confirmed this. The low and steady pressure profile generated by sand mix 5 is due to the sand permeability and lower level of fines (2.6%). There was no evidence of plugging during the tests, and good retention was achieved in each case. Sand-through, with time, demonstrated good overall retention performance, while pressure data were stable and matched the sand properties. There was no evidence to suggest that any plugging occurred with the sand tested.
However, it should be noted that while plugging can occur with any OCMP filter combination, there is still insufficient information to determine any specific criteria for a plugging risk to occur. The evaluation concluded that the OCMP filter had a positive effect on sand retention and delivered improved well performance.
Further examination. Retention tests examine overall trends with OCMP filter performance. The total sand-through in each test can be used to examine whether any correlation exists between a sand size parameter and sand retention by a given filter medium. The polymer filters being evaluated were depth filters, and so retention may be expected to correlate to the sand D50 value, as with gravel packs, rather than D10, as with metal mesh surface filters. It is important to note that gravel packs have largely mono-sized pores, whereas polymer filters have a range of pore sizes, and so different parameters are relevant in this case. Polymer filters were tested to give an indication of sand distribution at the end of the test.
It was not possible to definitively determine retention criteria from the data available in the initial developmental phase of the OCMP. However, based on results collected thus far, if the sand is large enough to be retained (as judged by the D50 value) then the amount of sand passing the polymer filter correlates to the fines content. When the concentration of fines is higher, compression of the OCMP creates a significant change to the retention capabilities.
As a result of conducting laboratory testing with single and multiple PPI filter combinations and compressing the material, which included an additional convergence layer, Tendeka repeatedly improved the performance and understanding of the downhole filter mechanism in new and challenging remedial environments, with both outcrop and reservoir sands.
Operational deployment. The Filtrex system was initially designed to be deployed, using coiled tubing. However, most through-tubing sand screen installations in Mahakam field are transported by slickline. Thus, a slickline version of the tool was developed. A packer was first pre-set at the pre-determined depth, using a casing-collar locator correlation below the OCMP filter to function as the anchoring system. The OCMP sand screen then latches into this packer. As soon as the tool has been latched and anchored, the running tool is functioned to release. Force and jarring are then applied to pull off and retrieve the compression sleeve and expose the OCMP filter. As no top packer is required on the three wells (Ax-1, Ax-2 and Ax-3), the perforation interval was designed so that the OCMP filter would have 1-2 ft of overlap, as shown in Fig. 6.
Results of technology deployment. Oil-producing well Ax-1 was identified as having a high risk of sand production and had an output target of 150 bopd. After deployment, the well test showed it was producing 600 bopd, sand-free. And within a five-month period, the recovery factor was up 155%.
Gas-producing wells Ax-2 and Ax-3, with deviations up to 58°, were then completed. Initial well test results showed production at 2.55 MMcfgd, sand-free. The target rate was 1 MMcfgd. Therefore, the tool exceeded expectations and outperformed results experienced with sand control treatments in similar wells. However, due to water breakthrough at 2.5 MMcfgd, after one month, both wells started to produce some sand.
After two months, well Ax-3 had recovery at 300% and was still producing sand-free at a lower rate of 1 MMcfgd. However, it was suspected to have a higher shale content than the other two wells, resulting in lower wellhead flowing pressure and is no longer producing. All wells were shown to have exceptionally low skin-aiding production. This was an unknown prior to the well campaign.

Spiral Screw Conveyor Due to the campaign’s success, the operator is planning to use the OCMP sand control tool as its primary sand control system in both cased and perforated reservoirs, eliminating the requirement to stock various micron-sized screens and gravel. The results of the three-well campaign have shown Filtrex has a high potential to outperform most of the developed sand control technologies utilized in Mahakam field.